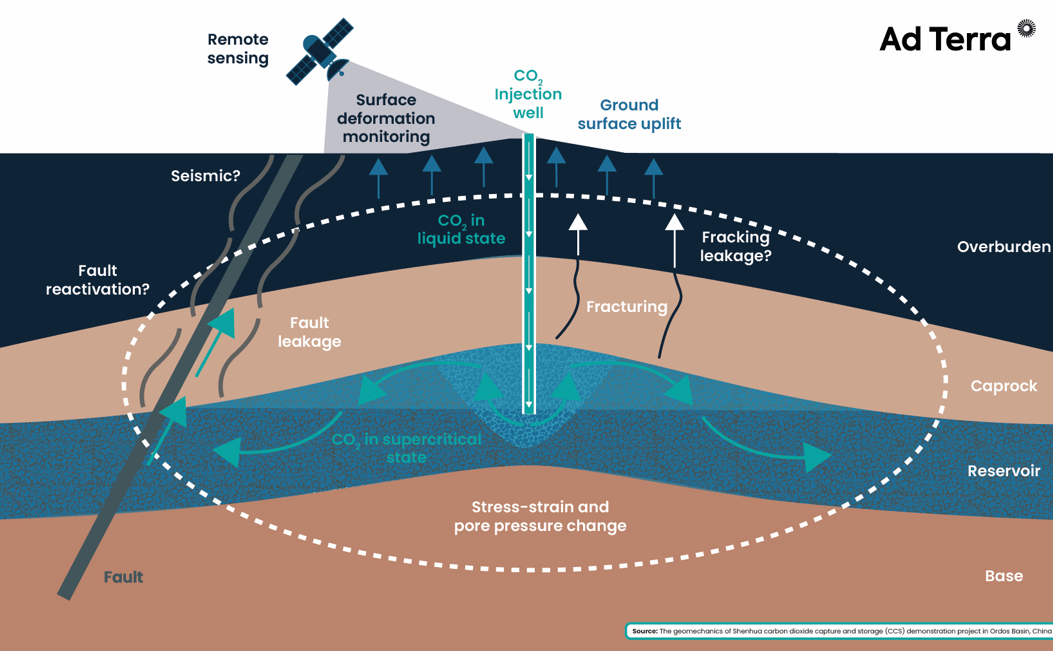
Carbon Capture Utilisation and Storage (CCUS) is at the heart of global efforts to mitigate climate change, offering a way to reduce hard-to-abate industrial CO2 emissions. The deployment of these solutions depends not only on their technical feasibility and commercial viability but also on building public confidence in the environmental safety of storing large volumes of carbon dioxide in underground geological reservoirs over the long term.
Public acceptance of such projects depends on showing robust safeguards against leaks and clear risk management protocols, making it vital for the industry to communicate its mitigation strategies clearly. Caprock integrity is essential for carbon storage success – any failure creates escape routes for CO₂, defeating the storage’s purpose and seriously hurting the environment.
When CO₂ is injected into a targeted reservoir deep underground during CCUS projects, the caprock acts as a barrier, preventing the upward flow of gases. It seals the CO₂ within the geological formation, miles below the surface. However, this barrier is not immune to change. The simple fact of injecting CO₂ increases the reservoir pressure, which places stress on the caprock. Over time, this stress can lead to the development of cracks or fractures, especially if the rock contains pre-existing geological weaknesses.
To identify where leaks could potentially appear, analysing how faults interact with the present-day stress field is fundamental[1]. Caprock stability maintenance represents both a technical imperative and an environmental safeguard. Engineers and scientists increasingly rely on geomechanics modelling to evaluate, monitor and safeguard the integrity of caprock in these projects[2][3]. Successful modelling depends on collecting detailed data regarding pore fluid composition, mineralogy, local stress conditions, fluid pressures, and any existing faults’ orientations and frictional properties[4].
Several factors pose a threat to caprock stability during CCUS operations. In addition to pressure, temperature differences also play a role. The injected CO₂ is often cooler than the surrounding rock, creating thermal stresses that weaken the caprock, similar to how sudden temperature changes can cause cracks in materials like glass. Furthermore, natural weaknesses in the rock, such as pre-existing faults or fractures, can become vulnerable under the pressures of CO₂ injection. Although these imperfections are often stable under normal conditions, they can be exacerbated by the stresses introduced during CCUS operations.
Given these potential threats, continuous monitoring of caprock integrity is essential before, during, and after CO₂ injection. To address these challenges, engineers use geomechanical models that simulate how subsurface formations behave under stress. These models enable scientists to predict how the caprock will respond to CO₂ injection, allowing them to identify and mitigate risks before they escalate. Two main types of models are used in CCUS projects: 1D and 3D geomechanical models. Each type offers unique insights into different aspects of the underground environment and plays a crucial role in monitoring caprock integrity.
1D geomechanical models provide a simplified, vertical snapshot of stress and pressure along a wellbore. Engineers typically use these models during the early stages of a project to evaluate how much pressure the caprock can withstand before fracturing. While 1D models are quick and cost-effective, they have limitations because they only capture stress in one direction, potentially missing more complex patterns in the rock.
On the other hand, 3D models offer a more detailed, full-scale view of stress distribution across an entire reservoir. These models integrate seismic surveys, well logs, and production histories to create a comprehensive simulation of the underground landscape. By simulating the long-term effects of CO₂ injection, 3D models help engineers identify potential weak points in the caprock before they become problematic.
Although 3D models require significant computational resources and investment, they provide critical insights, making them invaluable for large-scale CCUS projects. The detailed information they offer is essential for ensuring the long-term success of these projects.
As CCUS technology scales up worldwide, robust caprock integrity monitoring becomes central to project success. These storage projects rely on carefully selected geological formations with proven sealing capabilities, capable of safely containing millions of tons of CO₂ deep underground. Caprock monitoring underpins the effectiveness of CCUS operations. Verifying that CO₂ remains securely stored in its intended location is made through sophisticated engineering and monitoring systems.
The natural geological barriers beneath us serve as powerful climate allies in our action to remove hard-to-abate industrial emissions. CCUS technology, supported by rapid advances in geomechanical monitoring, demonstrates remarkable promise. As we accelerate our response to climate change, these underground storage solutions, backed by cutting-edge science and technology, represent a vital component in building a sustainable future.
Ad Terra has conducted caprock integrity studies across multiple sites:
Site A in a Northern Europe country
Ad Terra Consultancy completed a quick-look evaluation of caprock integrity for an underground storage project in Northern Europe. The evaluation uses effective stress regimes conforming to regional stresses. Our team established the proposed maximum allowable injection pressure based on the fracture closure pressure at the base of the caprock formation. To further mitigate the risk of fault slip, we conducted a 2D Mohr-Coulomb stability analysis.
Site B in a Middle East country
Ad Terra Consultancy constructed 1D Mechanical Earth Models (1DMEMs) for three key wells to evaluate stress profiles, reservoir stress paths, and caprock stress arching effects. Using geological, well log, and pore pressure data, our team established a safe operating pressure below the Fracture Close Pressure (FCP) and identified the pore pressure needed for fault reactivation. This analysis supports the field’s plan to use a carbonate/dolomite reservoir for CO2 storage, where pressure changes from injection will alter the stress equilibrium of the reservoir-caprock system. Our consultants assessed fault reactivation conservatively, applying a low friction angle and low cohesion, identifying the FCP criterion as the primary constraint. This initial phase delivers a conservative first estimate based on limited data. A more detailed 3D geomechanical model is being developed for the future phases.
About this article series
This article series highlights the role of Carbon Capture, Utilisation, and Storage (CCUS) in mitigating climate change and supporting the global energy transition. Each step of the process is examined, from CO2 capture technologies, transport challenges, utilisation opportunities, and geological storage options through caprock integrity considerations, operations monitoring and safety to commercialisation schemes. This series provides insights into how CCUS technologies can contribute to a sustainable future.
About the author
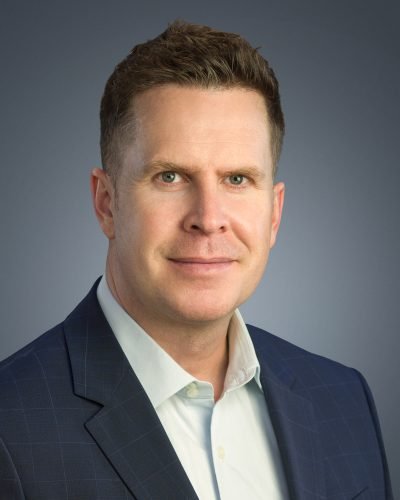
Kevin Webb is a Geomechanics Specialist with over 18 years of experience in the energy sector, specialising in areas such as Carbon Capture Utilisation and Storage (CCUS), subsurface geosciences, and renewable energy project management. Throughout his career, he has contributed his expertise to a variety of high-profile projects, including the Bifrost, Aramis and Northern Lights CCUS projects. In these roles, he was responsible for leading efforts in 1D, 3D, and 4D geomechanical modelling, focusing on wellbore stability and risk assessments to ensure the containment of CO₂ during injection.
His technical proficiency spans across diverse subsurface challenges, including seismic interpretation, reservoir characterisation, and subsurface stress analysis. Kevin’s work has also involved developing innovative solutions to optimise wellbore designs and minimise risks in CO₂ sequestration. Beyond technical modelling, Kevin has played a key role in managing multidisciplinary teams and ensuring the integration of geomechanical insights into broader project strategies.
In addition to his geomechanics work, Kevin has shown a strong commitment to advancing renewable energy projects, applying his geosciences knowledge to the transition towards sustainable energy solutions. With a rich background in both conventional and renewable energy sectors, he stands out for his leadership and innovative contributions to geomechanics and CCUS geoscience.
[1] L. Chiaramonte, M. D. Zoback, J. Friedman, V. Vicki, Seal integrity and feasibility of CO2 sequestration in the Teapot Dome EOR pilot: geomechanical site characterization, 2007
[2] OSTI.GOV, J.W. Johnson, J.J. Nitao, J.P. Morris, Reactive Transport Modeling of Cap Rock Integrity During Natural and Engineered CO2 Storage, 2004
[3] HAL, Alba Zappone, Antonio Pio Rinaldi, Antonio Pio Rinaldi , Melchior Grab, Quinn C Wenning, Clément Roques, Claudio Madonna, Anne C Obermann, Stefano M Bernasconi, Matthias S Brennwald, Rolf Kipfer, Florian Soom, Paul Cook, Yves Guglielmi, Christophe Nussbaum, Domenico Giardini, Marco Mazzotti, Stefan Wiemer, Fault sealing and caprock integrity for CO2 storage: an in situ injection experiment, 2021
[4] J. E. Strait, R. R. Hillis, Estimating fault stability and sustainable fluid pressures for underground storage of CO2 in porous rock, 2005